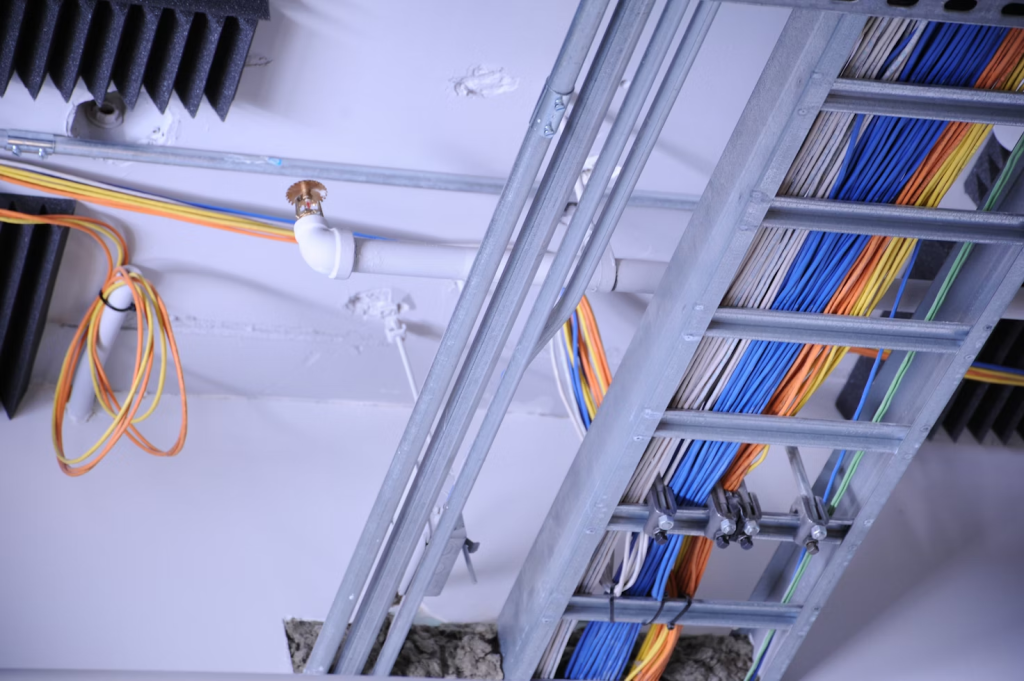
Key Takeaways
-
- Aluminum wiring background: Widely used in homes built in the 1960s and early 1970s due to rising copper prices. It was a cheaper alternative at the time.
-
- The problem is at the connections: The primary fire hazard with aluminum wiring isn’t the wire itself, but the connections at outlets, switches, fixtures, and within the electrical panel.
-
- Key issues:
-
- Galvanic corrosion: Occurs when aluminum contacts dissimilar metals, leading to corrosion and increased resistance.
-
- Aluminum oxide: A natural coating that forms on aluminum, which is highly resistant to electricity, causing heat buildup at connections.
-
- Expansion/contraction: Aluminum expands and contracts more than copper with temperature changes, loosening connections and increasing resistance.
-
- Key issues:
-
- High resistance = heat: All these factors lead to increased electrical resistance at connection points, which generates heat and can potentially ignite surrounding materials.
-
- Temporary fixes (limited value):
-
- Copalum connectors: Specialized crimp connectors.
-
- Twister Al connectors: Twist-on connectors.
-
- These are considered temporary repairs and don’t address the underlying issues with the aluminum itself.
-
- Temporary fixes (limited value):
-
- Permanent solutions (recommended):
-
- Complete rewiring with copper: The most thorough but most expensive option. Replaces all aluminum wiring.
-
- “Pigtailing” with copper: A more targeted approach where a short copper wire (“pigtail”) is connected to each aluminum wire end, moving the connection point to the copper.
-
- Permanent solutions (recommended):
-
- Insurance implications: Insurance companies are aware of the risks and may increase premiums, require remediation, or even refuse coverage for homes with unaddressed aluminum wiring.
-
- Professional help is essential: A qualified/licensed electrician is crucial for inspection, recommending the appropriate solution, and performing any work to ensure safety and code compliance. Do not go to just any general electrcian
-
- Frontline Pro Services: Offers expertise in assessing and remediating aluminum wiring issues
-
- Proactive approach: Contact an electrician to inspect the wiring of an older home.
________________________________________
Think for a moment about the electrical panel in your home. You probably don’t give it much thought, right? As long as the lights come on and your consumer products work, it’s all good. But in many older homes across the United States, there’s a silent aspect of the electrical connections behind your walls that might be cause for a closer look: we’re talking about aluminum wiring.
Back in the early 1960s, when the price of copper skyrocketed and pounds of copper started getting expensive, builders began looking for alternatives. Aluminum wire, lighter and less costly than traditional copper wire, seemed like a smart solution for residential construction. And so, aluminum wiring became a common type of wiring in branch circuits of homes built during that era.
Now, decades later, we understand there are some safety issues associated with this use of aluminum for home electrical connections. While aluminum conductors themselves aren’t inherently dangerous, under certain fire hazard conditions, particularly at the connection points, problems can arise. We’re talking about a potential risk of fire.
At Frontline Pro Services, we’ve encountered this issue in quite a few homes. We understand the concerns, and we’re here to shed light on aluminum wiring, explain the fire hazard, and most importantly, discuss the remediation options. Because understanding the potential risks is the first step toward ensuring the safety of your home and family.
Why Use of Aluminum in the First Place? The Story of the 1960s
To really understand aluminum wiring, we need a quick trip back in time to the early 1960s. Post-war America was booming. Residential construction was taking off, and with it, the demand for, well, everything – including copper wire.
Now, copper wire had always been the gold standard for electrical wiring. But suddenly, the price of copper started to climb – and climb fast. Think supply and demand, think global markets – all that economic stuff. For builders looking to keep costs down (and who isn’t?), copper wiring was becoming a significant expense.
Enter aluminum. A lighter metal, and crucially, at that time, significantly cheaper per pound of aluminum compared to pounds of copper. Solid aluminum wire emerged as an appealing alternative. It conducted electricity, it was readily available, and it promised substantial savings. For many builders, the use of aluminum seemed like a perfectly sensible, even innovative, move for branch circuit wiring. It was the original aluminum wire solution to a rising price of copper.
Why Aluminum Wiring Became a Fire Hazard
While the initial use of aluminum seemed like a practical solution at the time, over the years, some significant downsides emerged. It turns out that aluminum wire, particularly the solid aluminum wiring used back then, behaves differently than copper wire in ways that can, under certain circumstances, create a fire hazard. It boils down to a few key technical issues, mostly centered around the electrical connections.
Think of your home’s wiring as a network of pathways for electricity. Wherever wires connect – at outlets, switches, light fixtures, inside the electrical panel – those connection points are crucial. And that’s where the problems with aluminum wire connections often start.
First, there’s the issue of dissimilar metals. Many electrical connections involve different metals coming into contact. When you pair aluminum conductors with the metals commonly found in electrical devices (like switches and outlets), you can get galvanic corrosion. Imagine it like a tiny battery being created where the metals touch, leading to corrosion and a breakdown of the electrical connection.
Then there’s aluminum oxide. Aluminum naturally forms a coating of aluminum oxide when it’s exposed to air. This aluminum oxide layer is actually highly resistant to electricity. So, at those connection points, this oxide layer can hinder the flow of current, causing resistance.
And high resistance in electrical terms? That means heat. Like a lightbulb filament resisting electricity and glowing hot, these aluminum wire connections with high resistance can heat up significantly. If this heat builds up enough, especially in aluminum branch circuit wiring, it can become a serious fire hazard, potentially igniting nearby insulation or other flammable materials.
The Technical Dangers of Aluminum Wire Connections
We’ve mentioned that the trouble with aluminum wiring often centers around the electrical connections. But what specifically makes these aluminum wire connections so vulnerable? It comes down to a few interacting factors that can create real safety issues.
The core problem is high resistance. As we touched on earlier, the aluminum oxide layer, galvanic corrosion, and even just the expansion and contraction of aluminum can all contribute to increased electrical resistance at connection points.
Now, imagine electricity trying to flow through a point of high resistance. It’s like trying to push water through a narrow pipe – friction increases, and in the case of electricity, that friction manifests as heat. These connection points can start to heat up – sometimes significantly.
Think about the components involved in a typical electrical connection: the aluminum wire itself, the connection screws holding it all together, and the devices they’re connected to – outlets, switches, light fixtures, even a wire connector in some cases. If the proper torque on those connection screws isn’t maintained (and aluminum’s softness makes this tricky), if corrosion sets in, or if aluminum oxide builds up, that heat at the connection points intensifies.
Temporary Fixes: Solutions That Only Go So Far
If you’ve started looking into aluminum wiring issues, you might have come across terms like Copalum connectors or Twister Al connectors. These are often presented as ways to address the problem, and in some cases, they can be used as a temporary repair. But it’s crucial to understand what they are, and just as importantly, what they are not.
-
- Copalum Connectors: These are specialized crimp-style connectors designed specifically for aluminum to copper wire connections. The idea behind Copalum connectors was to create a more stable and reliable electrical connection point between the aluminum wire and, say, the copper wire leads of a device.
-
- Twister Al Connectors: Similarly, Twister Al connectors are another type of connector designed for aluminum wiring. They are twist-on style connectors intended to be used at connection points involving aluminum wire.
Now, while these connectors were developed to try and mitigate the risks, it’s important to be realistic. Using Copalum connectors or Twister Al connectors is often considered a temporary repair approach. They might help reduce the immediate fire hazard by creating a better electrical connection in the short term.
However, they don’t fundamentally change the nature of the aluminum wiring system itself. The underlying issues with aluminum, like its tendency to oxidize and its different expansion rate compared to other metals, remain. These temporary repair methods are generally not considered a permanent repair solution, and relying solely on them may still leave you with unresolved safety issues down the line. For any work involving even temporary repair solutions, consulting with a qualified electrician or licensed electrician is essential to ensure standards of practice and national electrical code compliance are followed.
Permanent Solutions: The Path to Long-Term Safety
For true peace of mind and lasting electrical safety, temporary repair methods simply don’t cut it. If you’re serious about addressing aluminum wiring concerns, you need to consider permanent repair options. There are two primary paths:
Complete Rewiring with Copper Wiring
This is the most thorough and definitive solution. It involves removing all aluminum wiring, including all branch circuit wiring, and replacing it entirely with brand-new copper wiring. Think of it as a complete electrical system upgrade. While it’s the most expensive and disruptive option, it eliminates the aluminum wiring issue completely and brings your home’s wiring up to modern standards of practice.
“Pigtailing” with Copper Pigtails
A more targeted, and often less costly, permanent repair involves “pigtailing.” This means a qualified electrician or licensed electrician will attach a short section of copper wire – a copper pigtail – to the end of each aluminum wire at all connection points. Specialized cu wire connector are used to ensure a safe and compatible connection between the dissimilar metals. This approach effectively moves all electrical connections away from the aluminum wire itself, minimizing the risks at those critical points.
Both of these permanent repair solutions should always be performed by a qualified electrician.
What About Insurance Companies? The Impact on Your Home Insurance
Here’s a practical reality to consider: insurance companies are well aware of the potential safety issues associated with aluminum wiring. They understand the risk of fire, and that awareness can impact your home insurance.
If your home is found to have aluminum wiring, especially solid aluminum wiring, you might face a few hurdles. Some insurance companies may increase your premiums to offset the perceived higher risk. Others might require you to undertake permanent repair options, like copper pigtails or complete rewiring, before they’ll even issue or renew your policy.
It really boils down to this: insurance companies are in the business of managing risk. Aluminum wiring, in its older forms, is often seen as a higher risk. Addressing aluminum wiring isn’t just about safety; it can also be about ensuring you can properly protect your home with adequate insurance.
Frontline Pro Services: Your Partner in Electrical Safety
Understanding aluminum wiring can feel overwhelming, but you don’t have to navigate this alone. At Frontline Pro Services, we have years of experience helping homeowners just like you assess and address aluminum wiring concerns.
Our team of qualified electricians are experts in identifying clad aluminum wiring, stranded aluminum wiring, and the older solid aluminum wiring. We understand the nuances of electrical load and national electrical code requirements. We can provide a clear, honest assessment of your home’s wiring and discuss the permanent repair options that best fit your needs and budget.
If you suspect your older home might have aluminum wiring, or if you simply want the peace of mind that comes with a professional inspection, reach out to Frontline Pro Services today. Let us be your partner in ensuring the electrical safety of your home and family.
Peace of Mind Through Proactive Action
The story of aluminum wiring in older homes is a reminder that sometimes, those “cost-saving” measures of the past can create unforeseen challenges down the road. The potential risk of fire associated with older aluminum wiring is real, but it’s also manageable.
The key takeaway? Don’t ignore the possibility. If you own an older home, being proactive is the smartest step you can take. A professional inspection by a qualified electrician is the first step towards understanding your situation and exploring the right permanent repair options for your home.
Electrical safety isn’t something to gamble with. Taking action now isn’t about fear; it’s about gaining peace of mind. And at Frontline Pro Services, we’re here to help you every step of the way, ensuring your home is safe and sound for years to come.
Frequently Asked Questions
What is the main safety concern with aluminum wiring?
The primary concern with aluminum wiring is not the wire itself, but the connections at outlets, switches, fixtures, and within the electrical panel. These connections can deteriorate over time due to issues like corrosion and expansion, creating fire hazards.
What causes the fire risk with aluminum wiring?
The risk arises from three key factors:
- Galvanic Corrosion: When aluminum contacts dissimilar metals, corrosion can form, increasing resistance.
- Aluminum Oxide: This coating naturally forms on aluminum and resists electricity, causing heat buildup at connection points.
- Expansion and Contraction: Aluminum expands and contracts more than copper with temperature changes, loosening connections and increasing resistance, which can generate heat and potentially ignite surrounding materials.
What are temporary solutions to aluminum wiring problems?
Some temporary solutions include:
- Copalum Connectors: Crimp-style connectors designed to improve aluminum-to-copper wire connections.
- Twister Al Connectors: Twist-on connectors designed for aluminum wire connections.
These solutions help improve the connection but don’t address the underlying issues with aluminum wiring.
What are permanent solutions for aluminum wiring?
Two permanent solutions are:
- Complete Rewiring with Copper: Replacing all aluminum wiring with copper. This is the most thorough but expensive option.
- Pigtailing with Copper: Connecting a short copper wire (pigtail) to each aluminum wire end at the connection points. This reduces the risks associated with aluminum wiring by moving the copper connection.
How can aluminum wiring affect my home insurance?
Insurance companies may raise premiums, require remediation, or refuse coverage altogether for homes with aluminum wiring, especially if the issues are not addressed. They consider aluminum wiring a higher risk due to the potential for fire hazards.